New wage management systems improve work environment
H&M group helps suppliers around the world to implement improved wage management systems in textile factories. This leads to better work environment as well as fairer wages – and in turn more motivated employees, which many employers within the textile industry realize is key to business success.
We want textile factories producing for H&M group to have a positive and motivating workplace environment. This not only benefits factory employees, but also to the same extent management and buyers such as H&M group. It’s a win-win – and a foundation for fair wages.
Our work is about making it possible for textile factories to be good employers.
Julia Bakutis, Sustainability Manager at the H&M group production office in Turkey
One prerequisite for a positive and motivating work environment are well-functioning wage management systems* ensuring that wages take everybody’s individual skills and experience into account. Equally important is that all factory employees know why they receive a certain wage and that they have a possibility for skill development – and that such development is rewarded. Likewise, it is crucial that there is a sound dialogue between employer and employees at the workplace. This is what H&M group’s work within this area is all about.
A new wage management system at ekpen tekstil
Ekpen Tekstil is one of around 500 textile factories implementing a new wage management system. The factory has worked together with H&M group’s local team in Turkey for two years to improve their wage management system. The factory with 200 employees is located in Denizli in western Turkey and has produced for H&M group for 16 years. It is now taking part in our program for strengthened wage management systems and improved workplace dialogue.
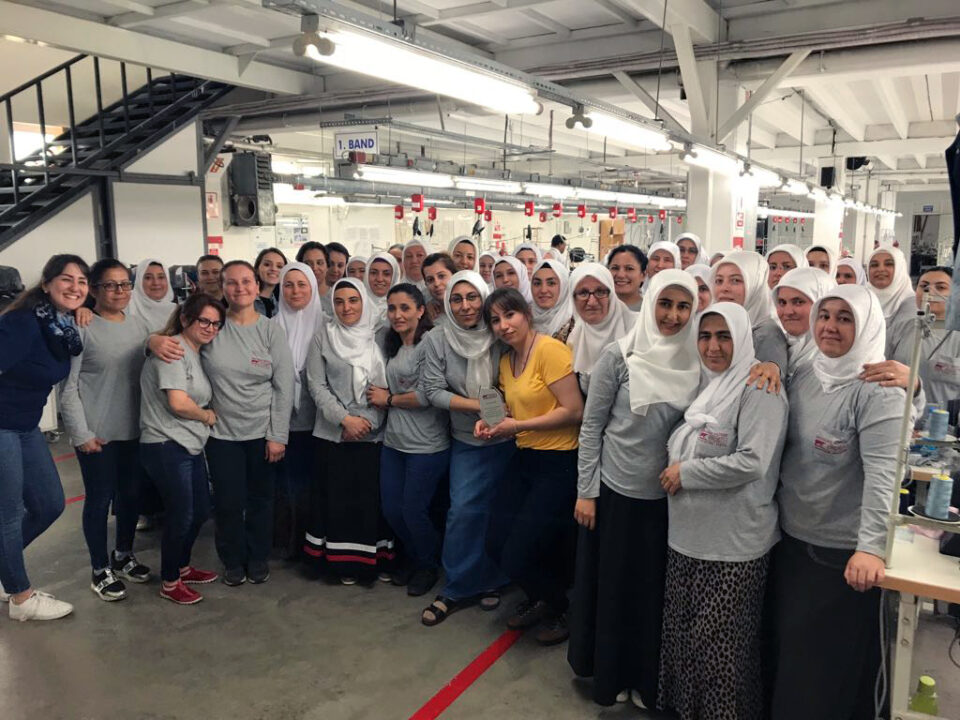
A wage reflecting skills and experience
Previously the employees at a factory could receive the same basic wage** even if their individual skills and experience differed. With the new, improved wage management system, implemented by factories such as Ekpen Tekstil, wages are now based on different parameters which create a fairer wage-setting. This new way of working has also resulted in that many factories now offer their employees skill development, which in turn leads to a happier work environment, and a possibility for motivated employees to earn a higher wage.
H&M group works to train suppliers in ten production countries; Turkey, Bangladesh, Cambodia, Indonesia, India, China, Myanmar, Vietnam, Ethiopia and Pakistan, on how parameters such as skills, experience and responibility should be included in wage management systems – and why this is important. Local teams from H&M group based in these countries support the suppliers and follow up on how the implementation of the wage systems is moving forward.
Employee voices from Ekpen Tekstile
“We try to create new ideas at work. I work in a more motivated way as I already know how my salary can be increased by my performance.”
“I worked in some other companies before and the salary was the same for all employees. I find the payment system in Ekpen quite fair. It is linked to the performance and effort, and open to workers’ feedback.”
“Our company owner declared during meeting this week that there will be a training line in the factory, and that scholarships will be given to those who enrolls in education. I will start open high school. I also want to join the training line and become a machine operator.”
Everyone should know how their wage is calculated
Factories participating in H&M group’s program ensure that workers have relevant knowledge about their wage; for example what the wage is based on, national minimum wages, legal regulations and overtime compensation rules. This decreases the risk of misunderstandings and makes it possible for the employees to check if they receive the correct wage.
Management and employees in dialogue
Before the work to improve wage management systems begun, the workplace dialogue at some factories was more or less non-existent, which led to misunderstandings and conflicts. H&M group is therefore supporting suppliers to create a well-functioning dialogue between employers and employees. This has resulted in more than 600,000 textile workers around the world now having democratically elected worker representatives that speak on their behalf in work-related matters. This is also the case at Ekpen Tekstil, where meetings every other week are now held between management and worker representatives allowing the workers to raise problems at the workplace as well as suggestions on improvements. For example, Ekpen Tekstil has involved worker representatives in the discussion on which parameters the wage should be based on and what kind of skills development should be offered.
Motivated employees – a business success
H&M group has noticed a mind shift; many factory managers are nowadays well aware of that motivated employees is key to success. It is a well-known fact that the chance of keeping trained and qualified staff increases if you are considered an attractive employer.
“I believe this system makes the workers aware of their contribution to the company through their work, but also of that they can have a career plan and develop through vocational training. It gives workers more opportunities and increase their trust in the company. It also contributes to a happier work environment as well as improved productivity”, says Ahmet Yavuçehre, owner of Ekpen Tekstil.
“Our work is about making it possible for textile factories to be good employers. The steps taken by Ekpen Tekstil to implement wage management systems taking employees’ individual skills, education and experience into account, supported by open and constructive communication, contribute to a more positive work environment. It’s a win-win situation for everyone”, says Julia Bakutis, Sustainability Manager at the H&M group production office in Turkey.
*H&M group supports suppliers’ implementation of improved wage management systems through the Fair Wage Method and the Wage Management System Method.
** Wage excluding overtime compensation.
Goals 2018
One of our goals by the end 2018 is for the supplier factories we work with the most through long-term partnerships (representing 50% of our product volume) to have stable and transparent wage management systems ensuring that wages that take worker’s skills, experience, performance and responsibility into account.
Another of our goals by the end 2018 is for the supplier factories we work with the most through long-term partnerships (representing 50% of our product volume) to have democratically elected representatives in place who can speak on behalf of the workers.