H&M Group’s journey towards becoming circular and climate positive includes exploring more sustainable materials. During 2020, H&M Group’s Circular Innovation Lab explored cutting-edge innovations such as carbon-negative materials, which remove more CO2 from the air than they emit.
Our Stories
Converting greenhouse gases into new materials
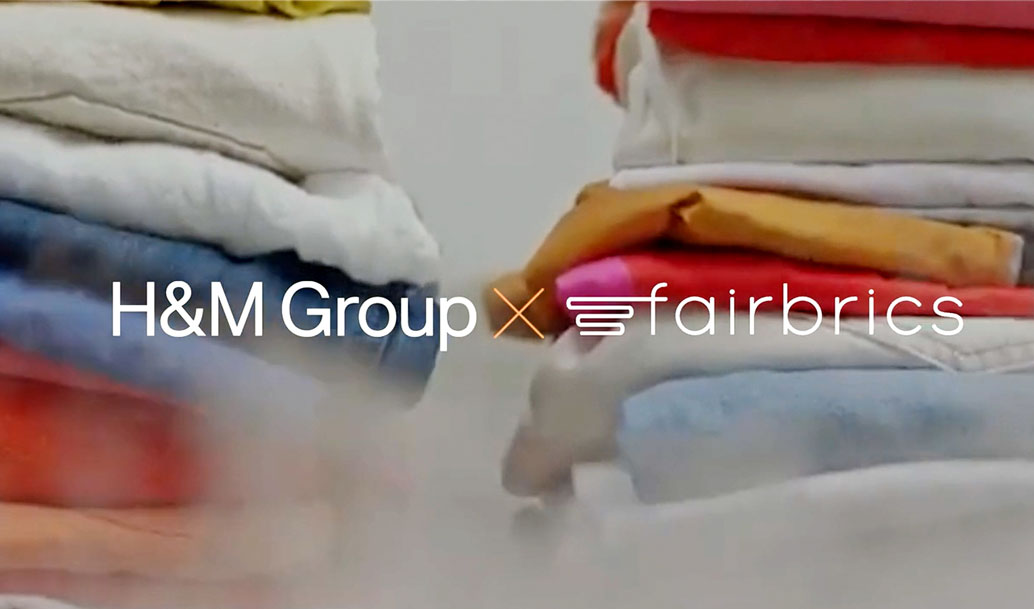
Watch how emissions are turned into new fashion materials.
In 2020, 64,5% of the materials used by H&M Group were either recycled or sourced in a more sustainable way. To reach the goal of 100% by 2030, the group continuously keeps up to date with the latest research and developments, for example by connecting with inventive start-ups, some of them through H&M Foundation’s innovation challenge Global Change Award.
H&M Group’s Circular Innovation Lab is dedicated to investigating innovative and more sustainable materials as well as assuring that they can be upscaled in higher quantities and used in large-scale production.
“The goal is to find and test more sustainable materials that our brands will be able to use continuously in their collections”, says Mattias Bodin, Circular Innovation Lab Lead at H&M Group.
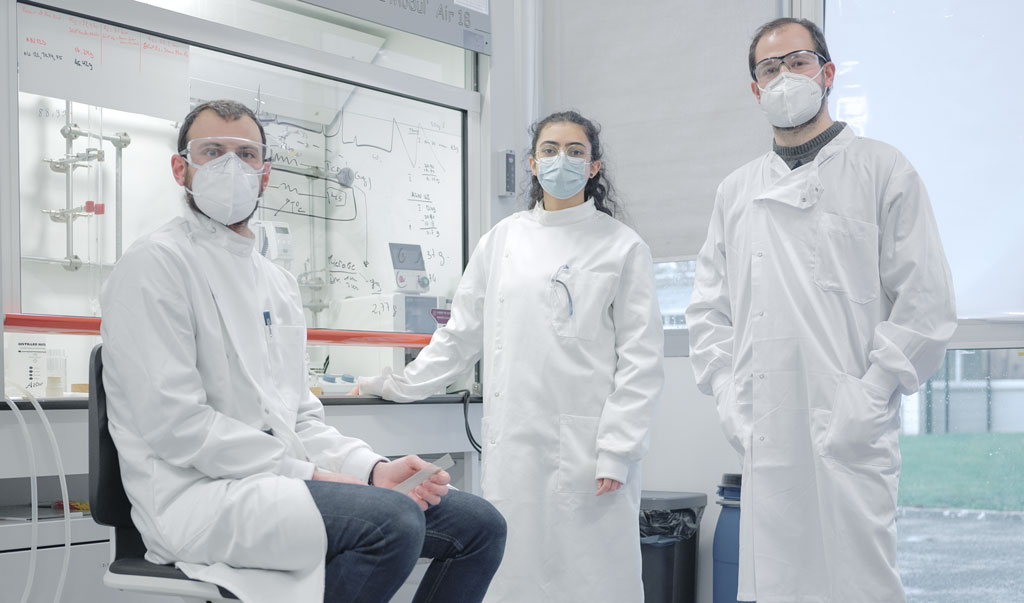
Exploring cutting-edge materials in French start-up Fairbrics’ laboratory.
The goal is to find and test more sustainable materials that our brands will be able to use continuously in their collections.
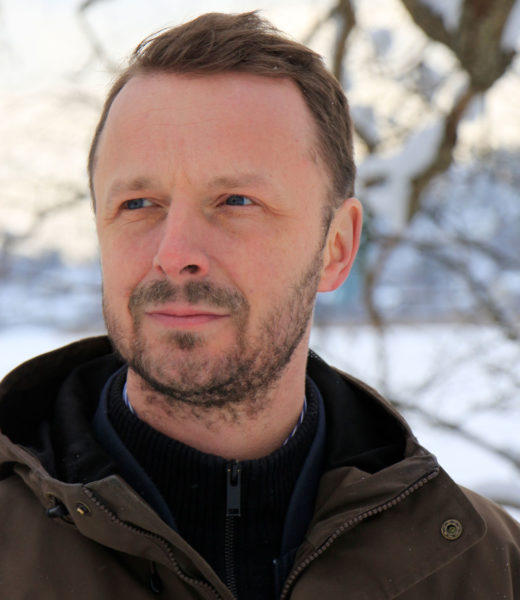
Mattias Bodin, Circular Innovation Lab Lead, H&M Group
Exploring carbon-negative materials
Carbon-negative materials, which remove more CO2 from the air than they emit, are new cutting-edge areas that have raised the interest of the Circular Innovation Lab.
The 2020 Global Change Award winner Fairbrics is a startup that has invented what could be the first carbon-negative synthetic fibre partly made of CO2 emissions.
This could potentially be an alternative to conventional fossil-based polyester. The Circular Innovation Lab is currently exploring how Fairbrics’ technology can be used to produce the first fabric for the group.
Another example is Berlin-based Made of Air, which essentially converts greenhouse gases into usable material by transforming waste residues from the wood industry into a carbon-negative compound that can replace plastic in a variety of applications.
The new material was used to make the sunglasses in the H&M Conscious Exclusive AW20 Collection.
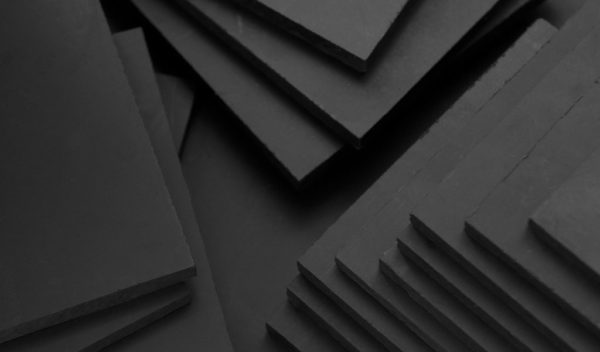
This plastic-like material from H&M Group’s partner Made of Air, is actually storing carbon.
Turning waste into new fibres
Other interesting projects include the development of a sustainable fabric made with the regenerated textile fibre InfinnaTM produced by Infinited Fiber Company.
The Finnish startup’s technology can turn cotton-rich textile waste, cardboard and agricultural by-products into unique new textile fibres with a soft and natural look and feel.
After a successful test, H&M Group invested in the Infinited Fiber Company in 2019. As a result, in early 2021, the first garments – regenerated from 100% post-consumer textile waste – were launched in Weekday’s online store.
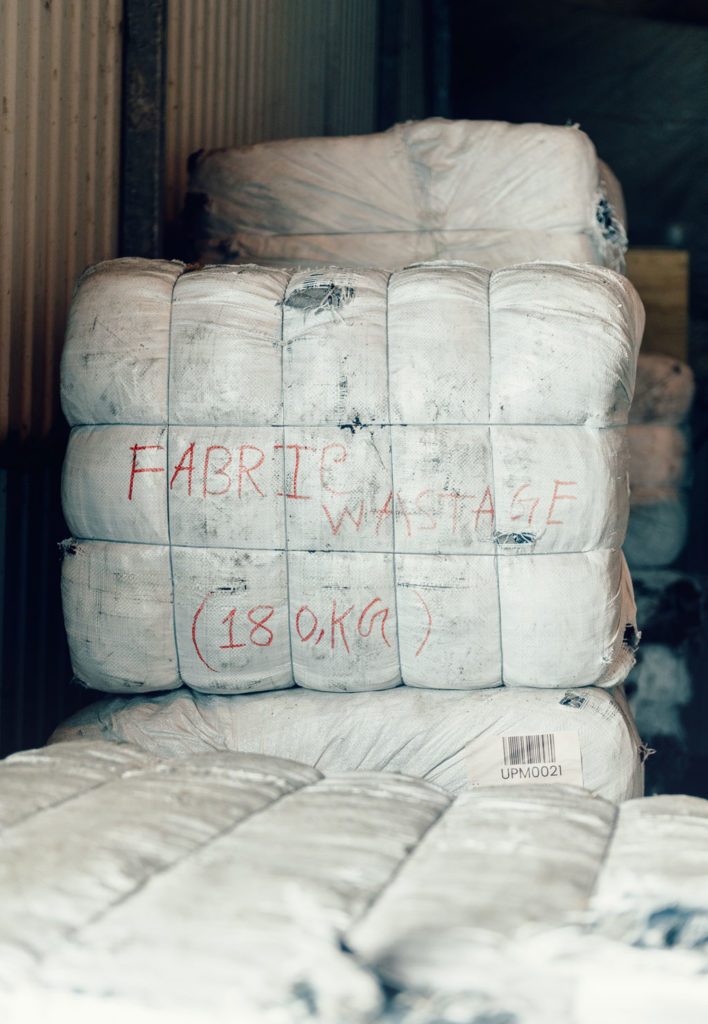
Partnering up further with the textile recycling company Renewcell.
In 2020, H&M Group also expanded its partnership with Renewcell by investing a further SEK 80 million (about USD 9.3 million) in the groundbreaking innovative Swedish textile recycling company.
Renewcell produces Circulose®, a dissolving pulp product made from unusable textile waste. The pulp is used as raw material for fibre production in H&M Group’s garment-making supply chain. Over a five-year period, Renewcell will provide H&M Group with tonnes of its pioneering virgin quality Circulose® fibres.
“The goal with our work is to find sustainable materials that the whole fashion industry can benefit from. As demand for these materials grows, they will also become more competitive”, says Martin Ekenbark, Circular Innovation Lab Project Manager at H&M Group.
Related
Download the full Sustainability Performance Report 2020.