The future of fashion depends on innovative materials that make use of what we already have, rather than taking more virgin resources. At H&M Group we’re always looking out for up and coming fashion innovations that we can use in our collections, but how do we find them?
News Article
Inside the H&M Group Circular Innovation Lab: How to make a garment out of thin air
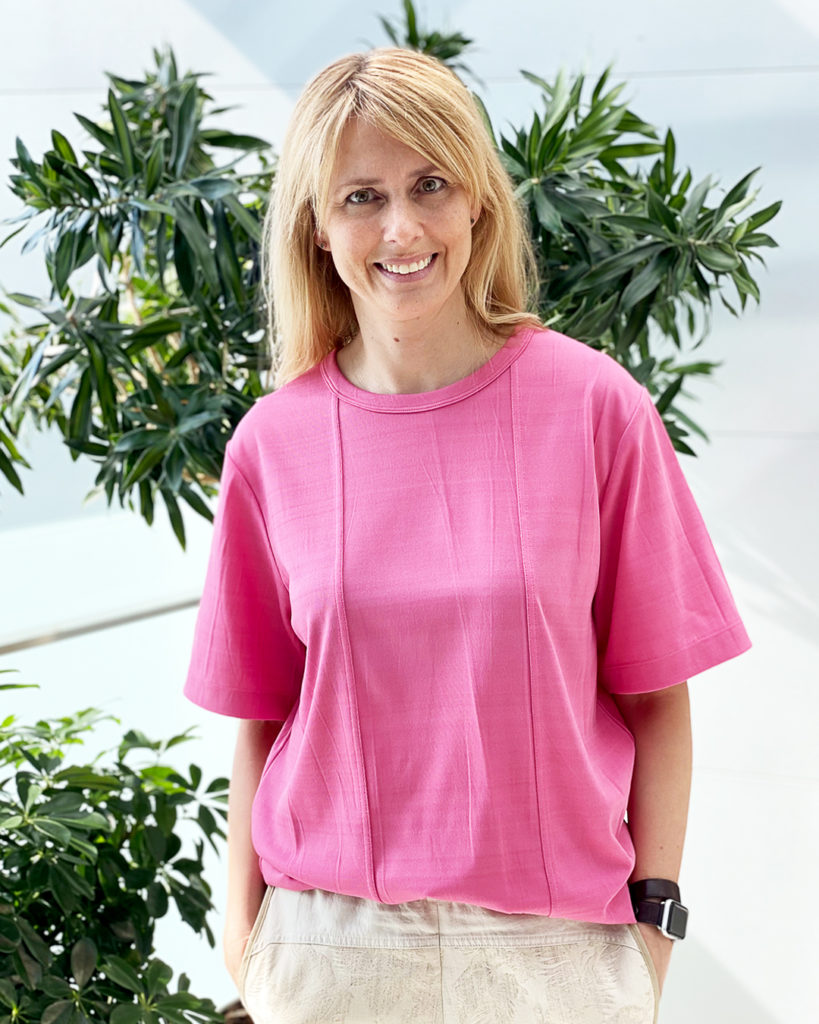
Helena Helmersson, CEO H&M Group, wearing a top made of thin air.
Last week Helena Helmersson, CEO H&M Group, took part in Fashion CEO agenda. At the event she wore a pink t-shirt The garment looks exactly like an ordinary top, but the fibres are literally spun from thin air. The fabric is developed by the French company Fairbrics with help from H&M Group’s Circular Innovation Lab (CIL).
Set up two years ago and based in Stockholm, the CIL helps early-stage start-ups navigate the transition towards becoming fully-fledged, production-scale companies. Innovators get help testing their ideas, insight on working with the fashion industry and access to our supply chain network. In return we discover new materials and processes that we can use in our collections.
“Alternative materials are key to for us to reach our goal of using only recycled or sustainably sourced materials by 2030. However, many of the materials we need do not exist today or are not available at a big enough scale. We need to speed up development and that’s what we’re here to do”, says Mattias Bodin, Circular Innovation Lab Lead.
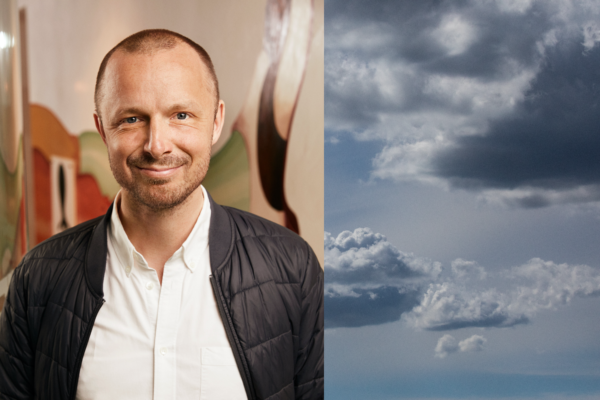
Mattias Bodin, Circular Innovation Lab Lead, H&M Group.
Turning pollution into yarn
Polyester is one of the most used fabrics in the fashion industry. However, conventional polyester is fossil fuel based and depletes resources as well as contributing to CO₂ emissions. Fairbrics tackles this head on by capturing CO2 from industrial emissions and converting it into polyester pellets using molecular chemistry. These pellets are then spun into polyester fibres and yarn that can be used in clothing.
“Like with all our projects, the first step was to make a proof of concept. We partnered with Fairbrics to produce small amounts of polyester using their technology. Then the volume was increased and when it worked well, we turned the polyester into a garment. By building up this way, we can assess the quality, processability and suitability for H&M Group brands”, says Mattias Bodin.
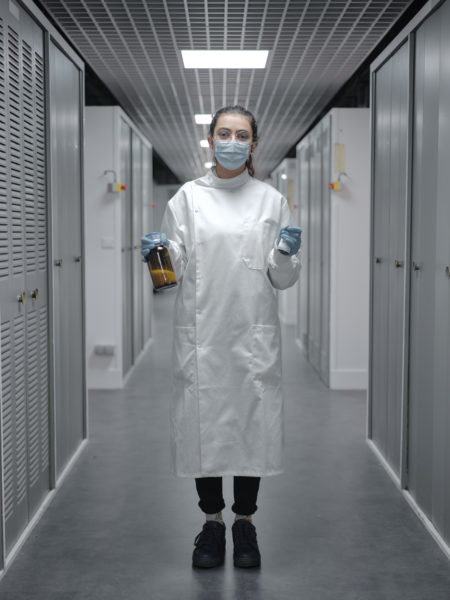
H&M Group partnered with Fairbrics to produce small amounts of polyester using their technology.
Removing innovation barriers
But innovation isn’t always an easy journey. When you’re developing unproven technology, problems can arise at any time. Plus finding the right partners or accessing funding is difficult when you’re just starting out. To remove these barriers, H&M Group has built an ecosystem that offers support in different ways:
- H&M Foundation’s Global Change Awards finds, supports and scales-up disruptive early-stage innovations.
- H&M CO:LAB invests in developing technologies that will help H&M Group becoming more circular.
- The Circular Innovation Lab (CIL) co-funds proof of concept project to test and evaluate technologies’ suitability for the H&M Group. They always have around 10 to 15 projects on the go at one time, all at different stages of development.
- Our H&M Group portfolio brands (H&M, COS, Weekday, H&M HOME, Monki, & Other Stories, ARKET) offer a clear route to market.
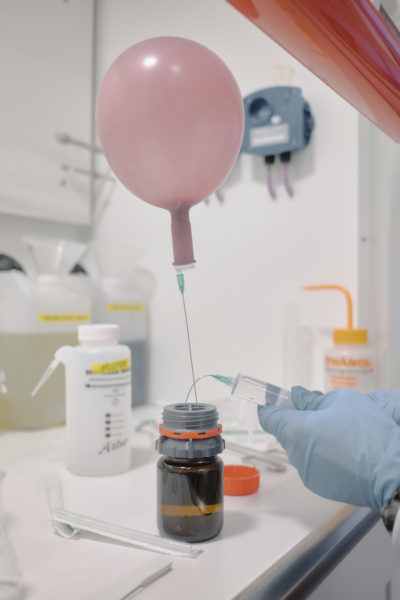
Inside Fairbrics’ laboratory. After just under a year the collaboration between Fairbrics and H&M Group has produced a fabric made of approximately 30 percent CO2.
Collaboration towards a sustainable future
“Fairbrics is a great example of how a company can benefit from our ecosystem”, says Mattias Bodin. “When we first heard about them it was too early for us to help them in the Circular Innovation Lab. That’s why we put them in touch with the H&M Foundation and encouraged them to apply for the Global Change Award. After they won in 2020 and went through the accelerator programme, we were able to step in to help Fairbrics to the next stage”.
After just under a year the collaboration between Fairbrics and Circular Innovation Lab has produced a fabric made of approximately 30 percent CO2.
“Producing our first samples has been an incredible journey. It took almost seven years and the hard work of a team of over 10 people between when we started to work on the chemistry and when we were able to touch and feel the fabric”, says Benoît Illy, Co-Founder and CEO at Fairbrics.
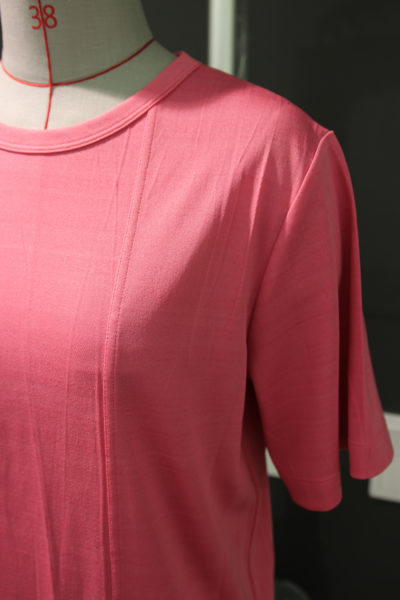
Close up of seam detail on the game-changing top.
The next step
Fairbrics and the Circular Innovation Lab have proven that greenhouse gases can be converted into raw materials for use in consumer products. However, we won’t be seeing garments made of CO2 hanging on rails in stores quite yet.
“Now we’ve proven the idea, the next step is for Fairbrics to launch a pilot project to produce larger quantities before scaling up to full industrial production”, explains Mattias Bodin.
Benoît Illy from Fairbrics reflects on the experience, “Working with Circular Innovation Lab has been an amazing experience. They were ready to invest time and energy for developing a long-term solution at a very early stage, when we are able to produce only a few grams. They were understanding of our challenges and very keen to give insights about textile manufacturing”.
Meet the makers
Our inhouse atelier team, which normally works with samples for our collections, took on the task to transform the highly innovative fabric into a garment. Working with Helena Helmersson they came up with a design classic that made the most of the fabric and showed off its drape.
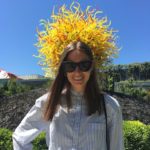
Malin Dubois, Designer
“I knew that the fabric was a big breakthrough for us and that the Circular Innovation Lab had been working on this project with our partner for some time. The fabric has a natural drape and reminds me of a mercerised cotton. It also has a nice subtle shine.
“Since these were the first sample meters, the mission was to create a garment with limited resources. The fabric is tubular and 40 cm wide, so we needed to add seams to the garment to be able to achieve the design”.
“In this type of project, you really feel that we work as one team and all roles are an equal part of the process. From the design idea to deciding where to add seams every step has been done in collaboration with the pattern maker and seamstress. It’s been very fun to work like this and amazing that H&M are supporting new innovations within fabrics”.
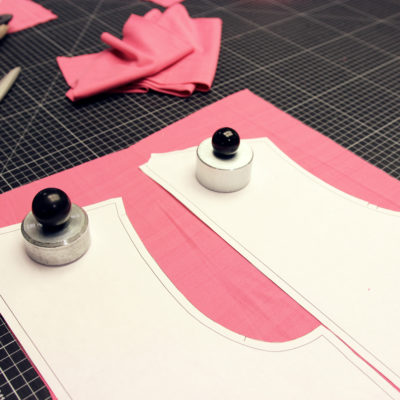
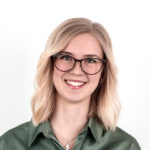
Ellinor Duda, Seamstress
“The fabric is quite narrow, so to place the pattern pieces when cutting is more challenging. And for this garment we only had enough fabric for one T-shirt, so I couldn’t afford any mistakes when cutting or sewing“.
“I was a bit nervous to work with it. As we only had one chance to get it right, I had to be extremely focused through the whole process. I double checked when cutting and I changed all the needles and cleaned the machines. To get an oil stain on it would have been a disaster”!
“We normally sew samples, so to sew a complete garment for a specific person and occasion is always exciting. To know what it will be used for and by whom, makes me want to give that little extra. I felt proud sewing the garment together, as I got to be a part of making something out of this sustainable and extraordinary fabric”.
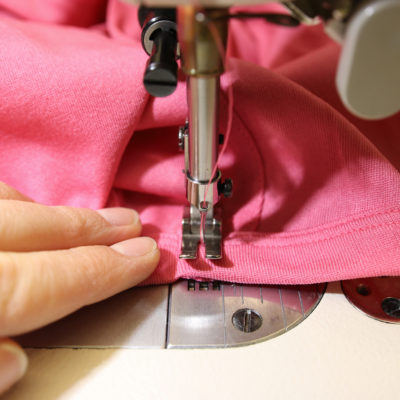
Circular Innovation Lab Success Stories
Alchemie Technology
H&M Group Circular Innovation Lab worked with Alchemie Technology to test their water-less dying technology. We supplied undyed fabric, which they dyed and sent to our supply chain partner who turned it into the first ever commercially available garments dyed using this technology. They are now possible to rent in H&M stores in Stockholm and Berlin.
Infinited Fiber Company
H&M Group Circular Innovation Lab supported Infinited Fiber Company to expand production of its regenerated cellulosic fibre, Infinna™ by testing and verifying its performance in our supply chain. This provided commercial quantities to Weekday for a February 2021 collection made from fabric containing half Infinna™ fibres and half organic cotton, the first time ever Infinna™ was available for fashion consumers.
Made of Air
H&M Group Circular Innovation Lab worked with Made of Air, which essentially converts greenhouse gases into usable material by transforming waste residues from the wood industry into a carbon-negative compound that can replace plastic in a variety of applications. The new material was used to make the sunglasses in the H&M Conscious Exclusive AW20 Collection.